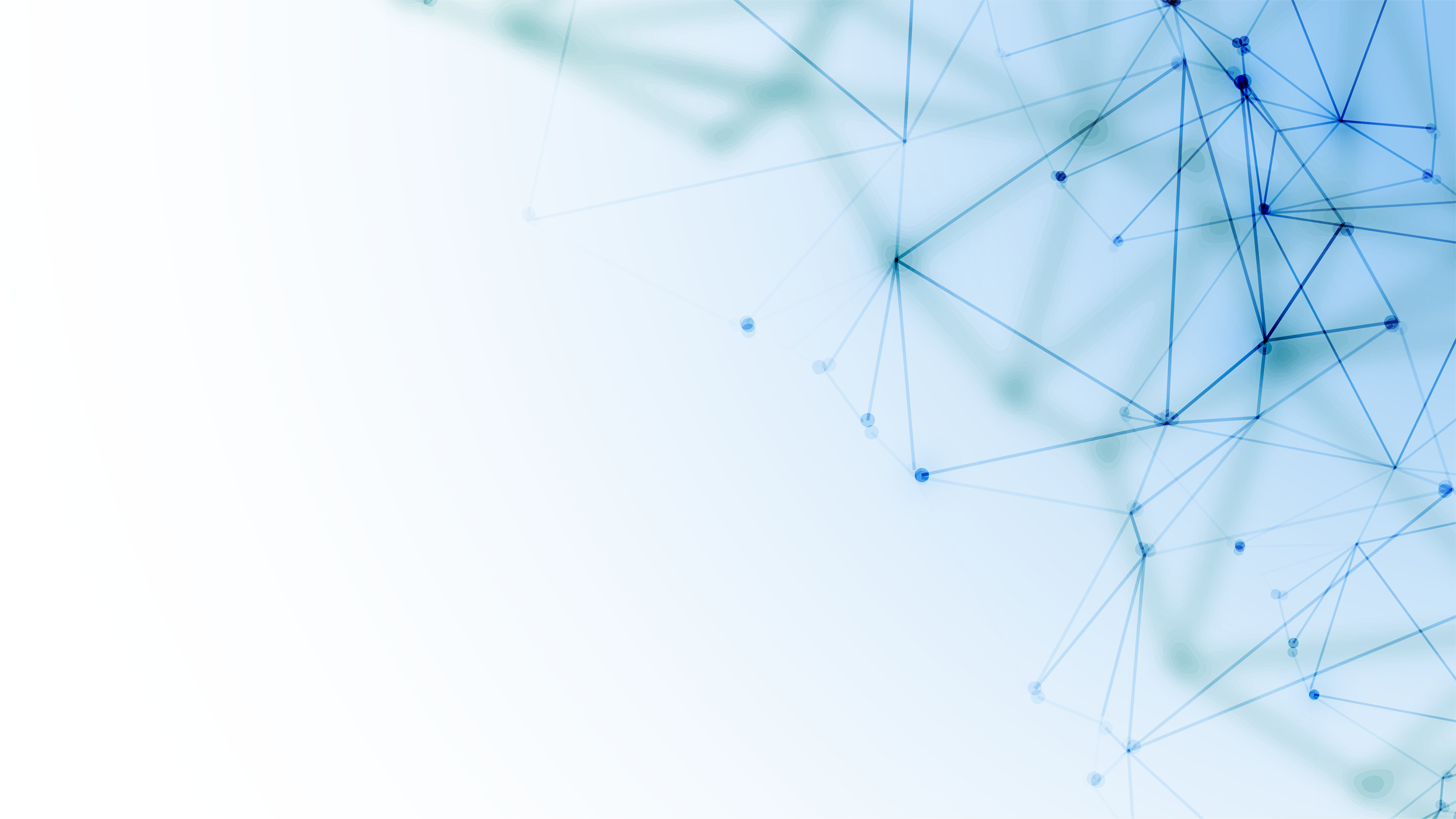
Overall Equipment Effectiveness (OEE)
Overall Equipment Effectiveness (OEE) measures how effectively your production assets are utilized, combining Availability, Performance, and Quality into one unified metric. Today, even a 5 % lift in OEE can translate into millions saved and substantial capacity unlocked.
Yet most factories routinely lose 20–30 % of throughput to unplanned downtime, speed losses, and scrap. Using our website and our OEE software, you’ll discover exactly how to calculate and benchmark your OEE, tackle the top five barriers to sustained improvement, and see how GlobalReader’s real-time tracking, predictive maintenance, and analytics suite drives rapid returns. Ready to pinpoint your biggest losses and turn data into action?
No financial commitment. Log in, take the tour, try it out!
The Three Pillars of OEE
Breaking OEE into its three core components helps you diagnose specific losses—and attack them with the right tools.
Availability
The percentage of scheduled time that equipment is actually running—downtime (both planned and unplanned) drags this down.
Learn more: Understanding the Six Big Losses in ManufacturingPerformance
How close your run rate is to the theoretical maximum cycle time—micro-stops and slow cycles chip away here.
Read: Real-Time Factory Data for Optimal Cycle TimesQuality
The ratio of good parts produced versus total parts—scrap, rework, and rejects all count against you.
See: Cost of Quality in Manufacturing
Learn how GlobalReader dashboards visualize each pillar in real time → Just check out our FREE DEMO. See Analytics Demo
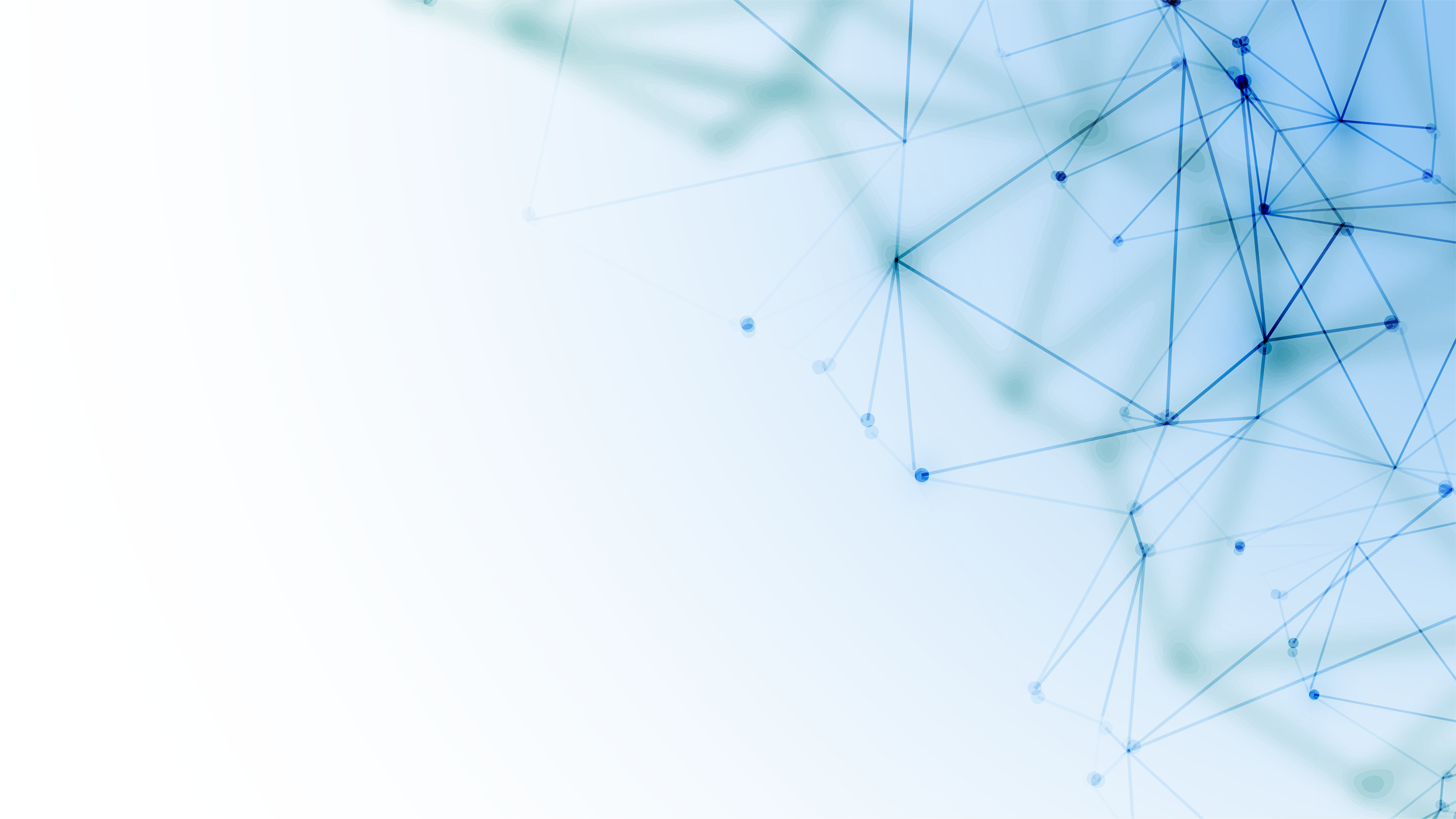
How to Calculate and Benchmark Your OEE?
Calculating OEE is straightforward: multiply Availability × Performance × Quality (each expressed as a percentage). For example, 76% availability × 90% performance × 95% quality yields an OEE of 65%. To benchmark:
Collect accurate runtime data
Compute each pillar separately
Multiply for overall OEE
Compare vs. industry norms
Our very user friendly OEE software helps you calculate this with ease. The setup is also very easy. We provide you with hardware (sensors) that you can install yourself or ask for our help. First you start off with our Analytics tool that’s included in the Starter Bundle. You can upgrade on the go. No big financial investment needed.
Common OEE pitfalls:
Ignoring micro-stops that add up to hours of lost production
Using theoretical cycle times instead of actual run-rates
Not resetting counters after planned maintenance
The Top 5 Challenges in Sustaining High OEE
Unplanned Downtime
Equipment failures and changeovers can halt production for hours if not proactively managed.Poor Data Collection
Manual logs and paper-based systems introduce errors and latency.Process Variability
Inconsistent setups and variable material quality create unpredictable performance.Siloed Reporting
When maintenance, operations, and quality use different tools, insights get lost.Low Operator Engagement
Without real-time feedback and incentives, even the best systems fail to deliver.
This can all be solved with GlobalReader OEE software
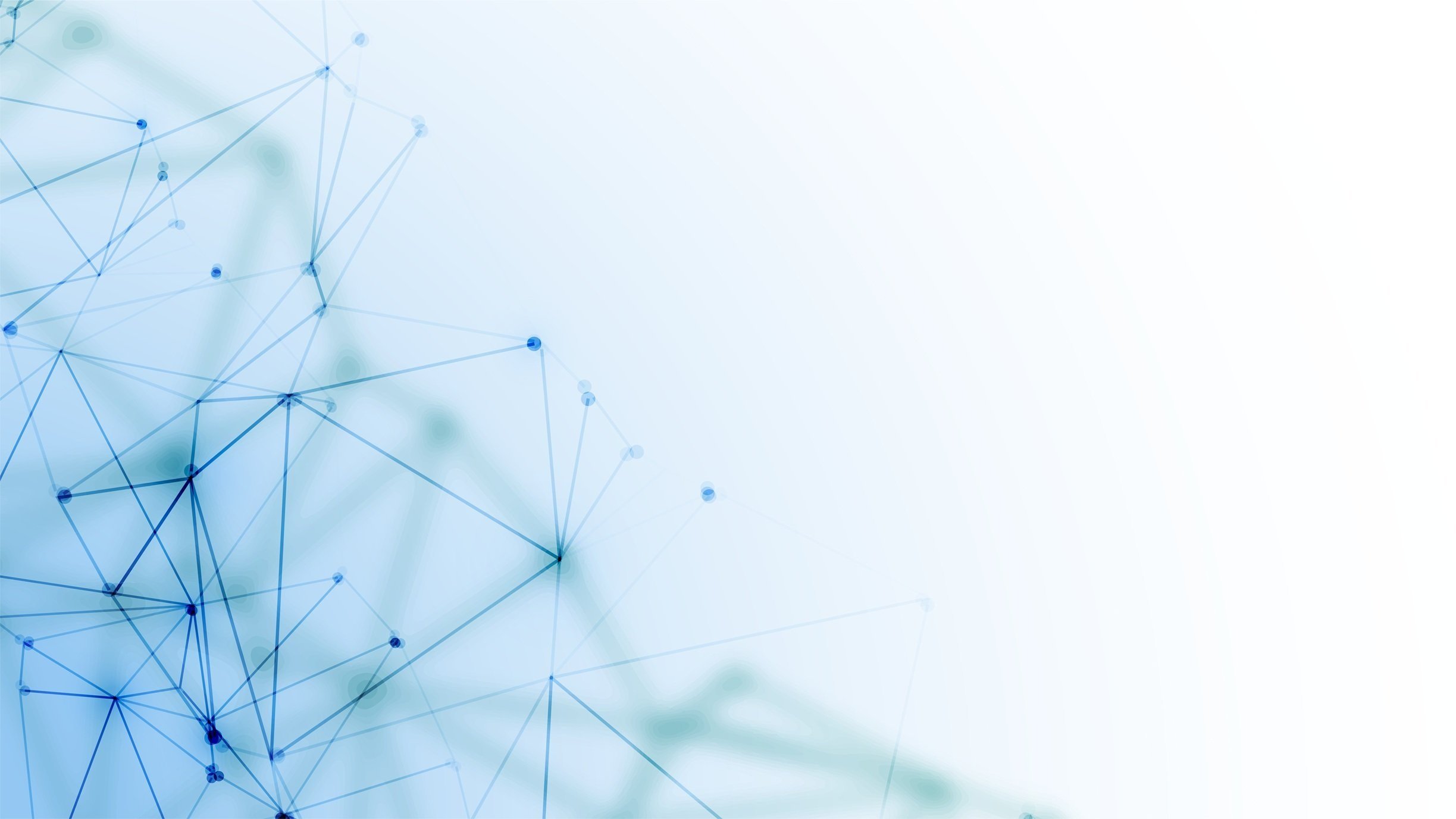
How GlobalReader Enables Continuous OEE Improvement
GlobalReader’s modular MES platform turns data into action at every step:
Real-Time Tracking
Automated capture of run/stopped states and reason codes in seconds → /features/operatorPredictive Maintenance
AI-driven alerts on vibration, temperature or cycle-count trends → /features/maintenanceAdvanced Analytics
Drill down from plant-wide dashboard to individual machine events → /features/analyticsProduction Scheduling
Optimize sequence, capacity and changeovers for max throughput → /features/planner
Typical payback: 2–4 months, with 10–25 % OEE gains.
OEE Frequently Asked Questions
-
In practice, 100 % is unattainable—minor stops and quality fluctuations are inevitable. Most world-class plants target 85–90 % as a stretch goal.
-
While OEE measures utilization of scheduled time, TEEP (Total Effective Equipment Performance) measures utilization of all calendar hours, including unscheduled time.
-
Reset counters at the start of each shift or production run to keep data clean—avoid carrying over scrap or downtime from previous batches.
-
Overall Equipment Effectiveness is calculated as the product of its three pillars:
OEE (%) = Availability (%) × Performance (%) × Quality (%)Each pillar is expressed as a percentage (0–100 %), and the result is also a percentage.
-
OEE stands for Overall Equipment Effectiveness—a single metric that captures how well your manufacturing equipment is utilized relative to its full potential.
-
Imagine a machine scheduled for 480 minutes/day:
Operating time (after downtime): 432 min → Availability = 432/480 = 90 %
Ideal cycle time: 1 min/part; actual output: 400 parts → Performance = (400 × 1 min)/432 min = 92.6 %
Good parts: 380 of 400 → Quality = 380/400 = 95 %
Then OEE = 90 % × 92.6 % × 95 % ≈ 79.3 %.
-
In a production setting, OEE quantifies the real-world efficiency of your machines by combining uptime, speed and quality into one figure. It highlights exactly where you lose capacity—so you can target improvements.
-
The Performance pillar compares actual run rate to the ideal rate:
sql
CopyEdit
Performance (%) = (Ideal Cycle Time × Total Pieces) ⁄ Operating Time × 100
It reveals losses from slow cycles and micro-stops.
-
An OEE calculator automates the formula, letting you enter uptime, cycle times and scrap counts to instantly compute each pillar and overall OEE. GlobalReader OEE software includes this and gives you the best overview of your OEE.
-
World-class plants often achieve 85–90 % OEE.
Mid-tier operations sit around 60–70 %.
Beginner sites may start as low as 40–50 %.
Use these benchmarks to set realistic improvement targets.