OEE software. Increase machine availability 30%.
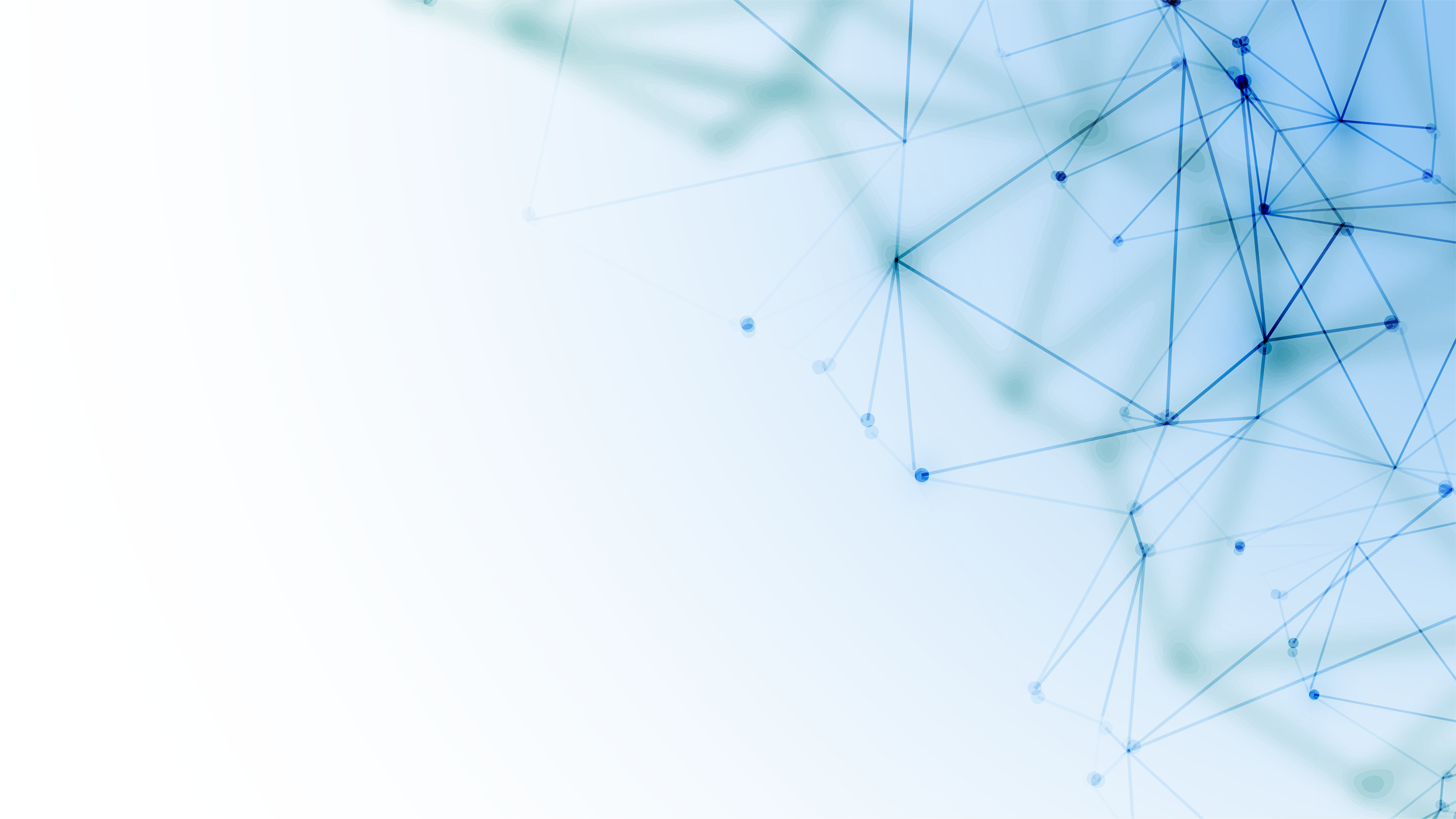
Real-time factory tracker
Where data drives: Decisions, Efficiency, Downtime, Quality, Visibility, Competitiveness.
GlobalReader software & hardware solution gives your factory real-time data on your production capacity. Increase your manufacturing machines availability, performance and quality with real-time factory tracking.
Bring decision-making from planning to real-time
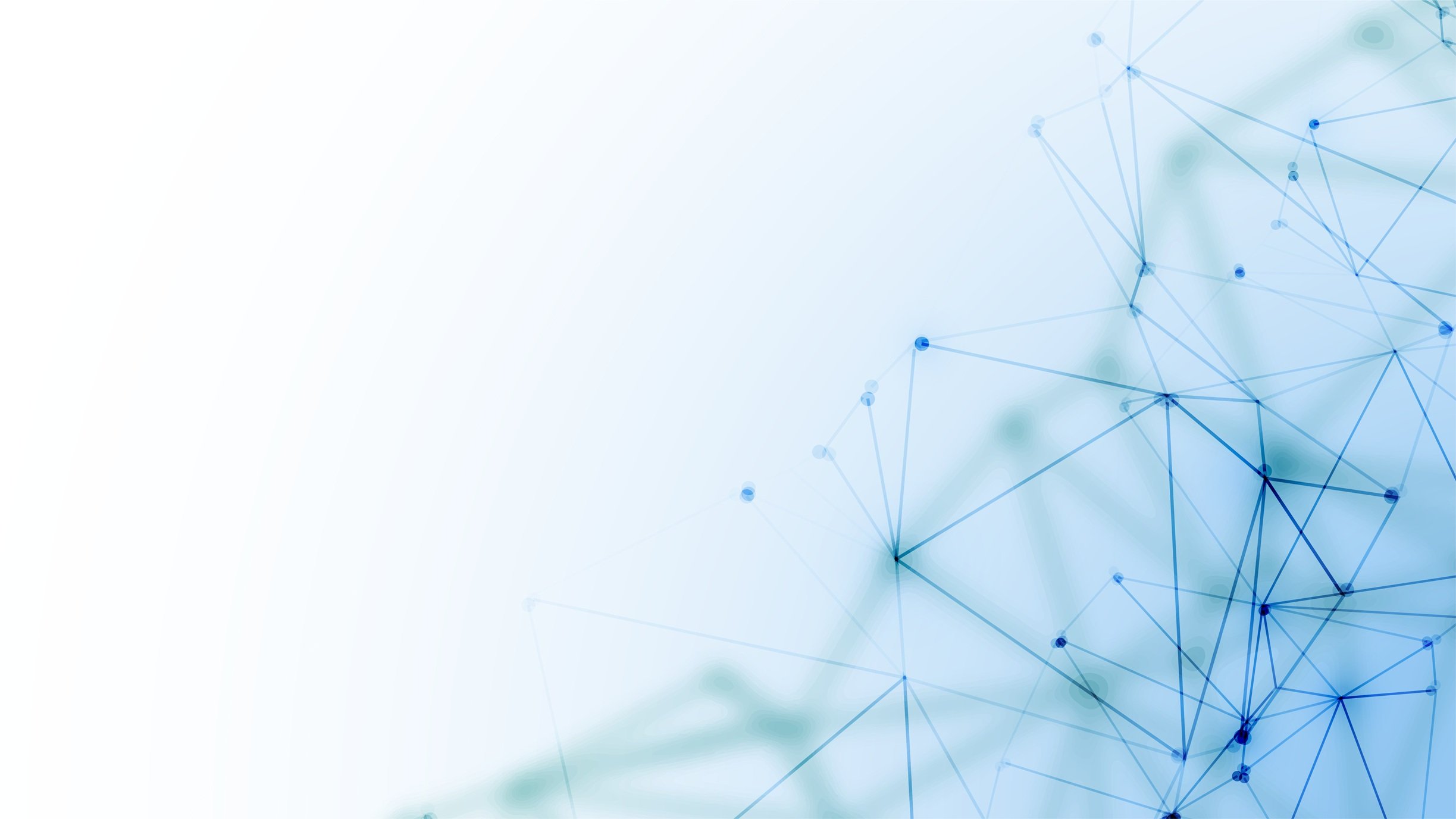
Collect real-time data
Your subscription includes both hardware and software, which can be easily set up by you or with assistance from our technicians.
Identify bottlenecks
Monitor real-time production and take immediate action. Later, analyse the data to understand discrepancies between actual performance and the production plan. GlobalReader collects and provides insights into these variations.
Customise
Explore GlobalReader array of extra features and add-ons designed for you. Enjoy custom reports, personalised production feedback, and tailored live views. Plus, seamless integration with your ERP systems.
Measure.
Analyse.
Improve.
with GlobalReader Software
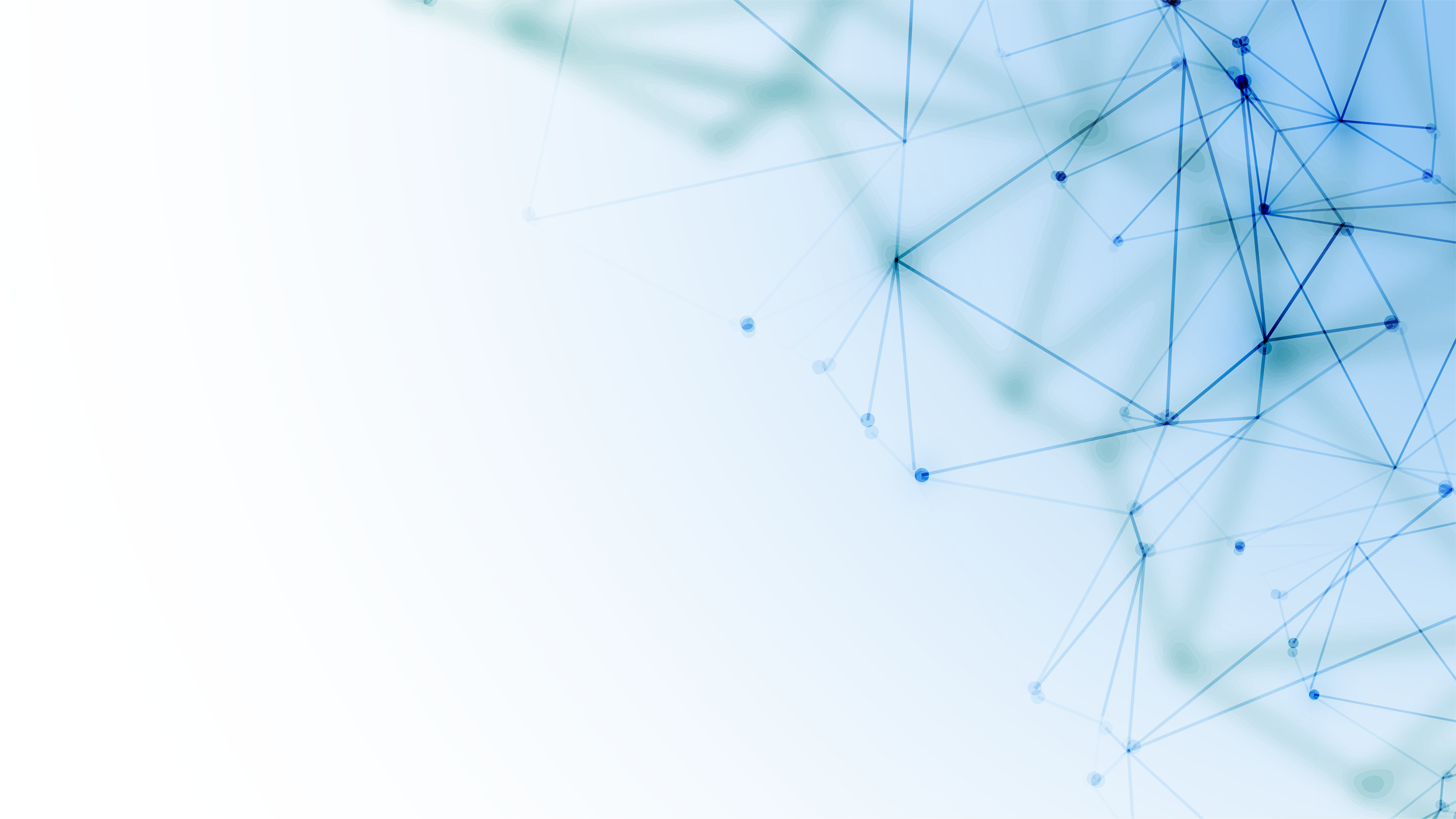
ANALYTICS
Real-Time Insights: GlobalReader Analytics likely offers real-time visibility into manufacturing operations, allowing you to monitor production performance, identify bottlenecks, and respond to issues as they arise.
Data-Driven Decision Making: With detailed analytics, you can make informed decisions based on historical data and trends, improving operational efficiency, reducing waste, and optimizing resource allocation.
Performance Tracking: Track key performance indicators (KPIs) such as Overall Equipment Effectiveness (OEE), machine downtime, and production output, enabling continuous improvement and strategic planning.
OPERATOR
Real-Time Data Collection: The Operator tool is designed to collect real-time data on downtime causes, machine operators, and the products being manufactured. This eliminates the need for manual record-keeping, significantly reducing errors in data collection and providing accurate insights into production processes.
Downtime Analysis: By allowing operators to instantly mark downtime reasons, this feature enables the capture of critical data on interruptions in real time. This data provides valuable insights into the root causes of downtime events, helping to identify recurring issues and implement proactive solutions to minimize downtime and maximize production output.
Elimination of Paper and Excel Sheets: The Operator feature replaces traditional paper and Excel-based data collection methods, reducing the administrative burden on manufacturing teams. This solves the problem of manual data entry errors, lost paperwork, and the need for time-consuming data consolidation, leading to more efficient and accurate production tracking.
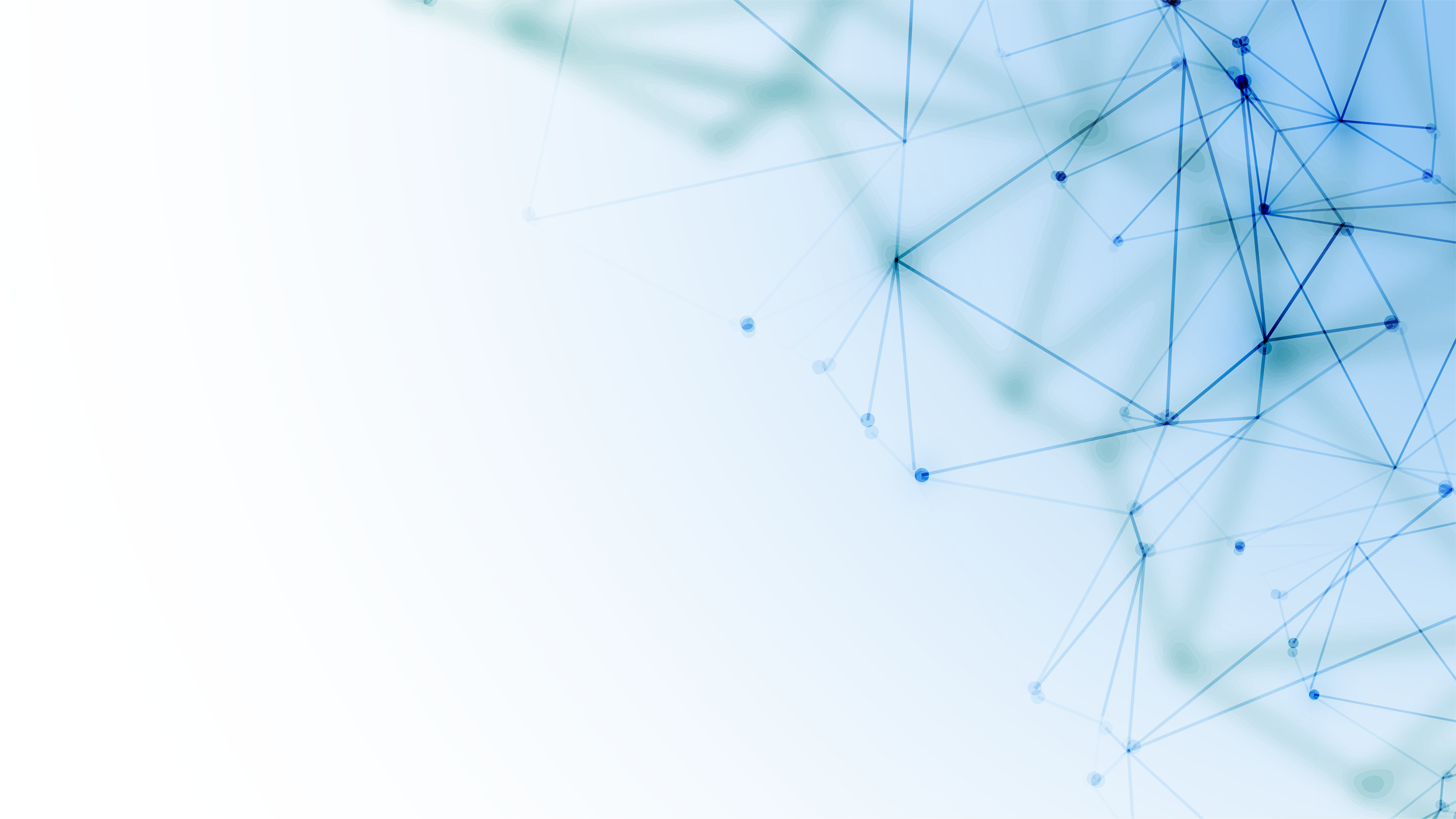
MAINTENANCE
Proactive Maintenance Approach: Streamlines maintenance tasks, allowing for efficient scheduling, monitoring, and optimization of technical work across workstations. This proactive approach ensures machinery operates at peak performance, reducing the need for reactive troubleshooting.
Efficient Scheduling and Technician Coordination: Offers a user-friendly system for technicians to easily access and follow their daily and weekly schedules. With clear day plans and notifications, the feature ensures timely completion of maintenance tasks, enhancing team efficiency and reducing the risk of missed tasks.
Comprehensive Spare Parts Management: Enables effective management of spare parts inventory and usage, tracking consumption for each maintenance task. This ensures that stocks are replenished in a timely manner, preventing delays due to parts shortages and contributing to overall operational efficiency.
PLANNER
Easily Manage Production Planning: Simplified production planning process by allowing for easy addition of orders, assignment of workstations, and real-time monitoring.
Efficient Work Allocation: Optimise tasks and schedules on machines, ensuring efficient allocation of work, reducing idle time, and maximising resource utilisation.
Increase collaboration: Boost overall manufacturing efficiency by integrating with other GlobalReader features. For example:
Notification: Instant alerts, if a downtime is detected, enabling to quickly rearrange orders across machines with drag-and-drop.
Maintenance: By sharing data with the Maintenance feature, it helps in incorporating maintenance tasks into production schedules, thereby minimising downtime and disruptions.
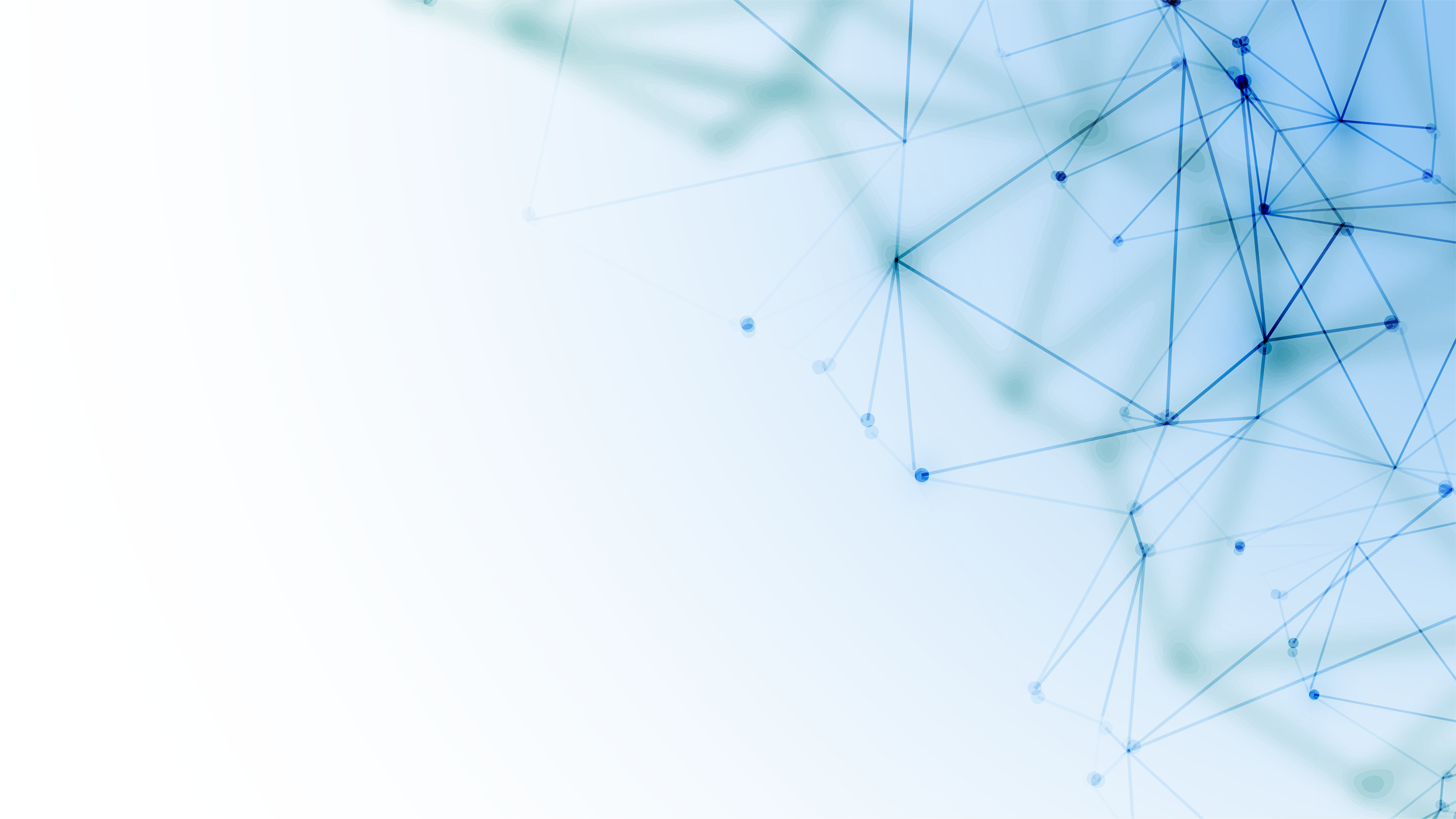
SMART FACTORY
Integration with ERP Systems: Flawlessly connect production machines and ERP systems and gain real-time visibility into manufacturing operations. Analyse data and generate reports to optimise your production.
Reduction of Errors: By connecting production machines directly with ERP systems, Smart Factory eliminates the need for manual data entry. This automation reduces errors and saves time, streamlining the data exchange between the shop floor and various systems.
Paperless Factory: Smart Factory supports a truly paperless environment by ensuring digital data flows between systems. This not only reduces the reliance on paper-based documentation, thus cutting costs, but also supports a more sustainable and greener manufacturing approach.
Trusted by manufacturers:
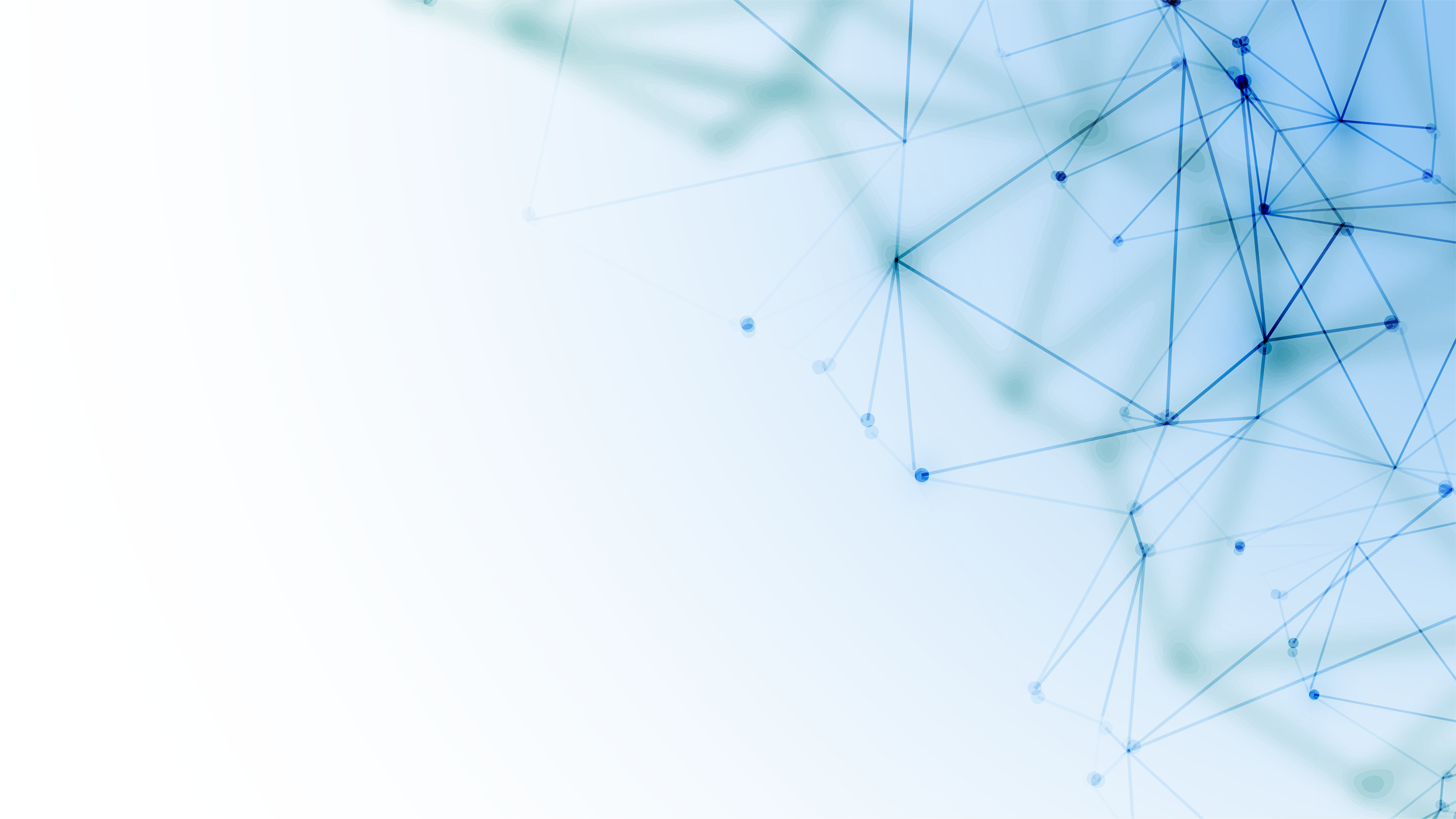